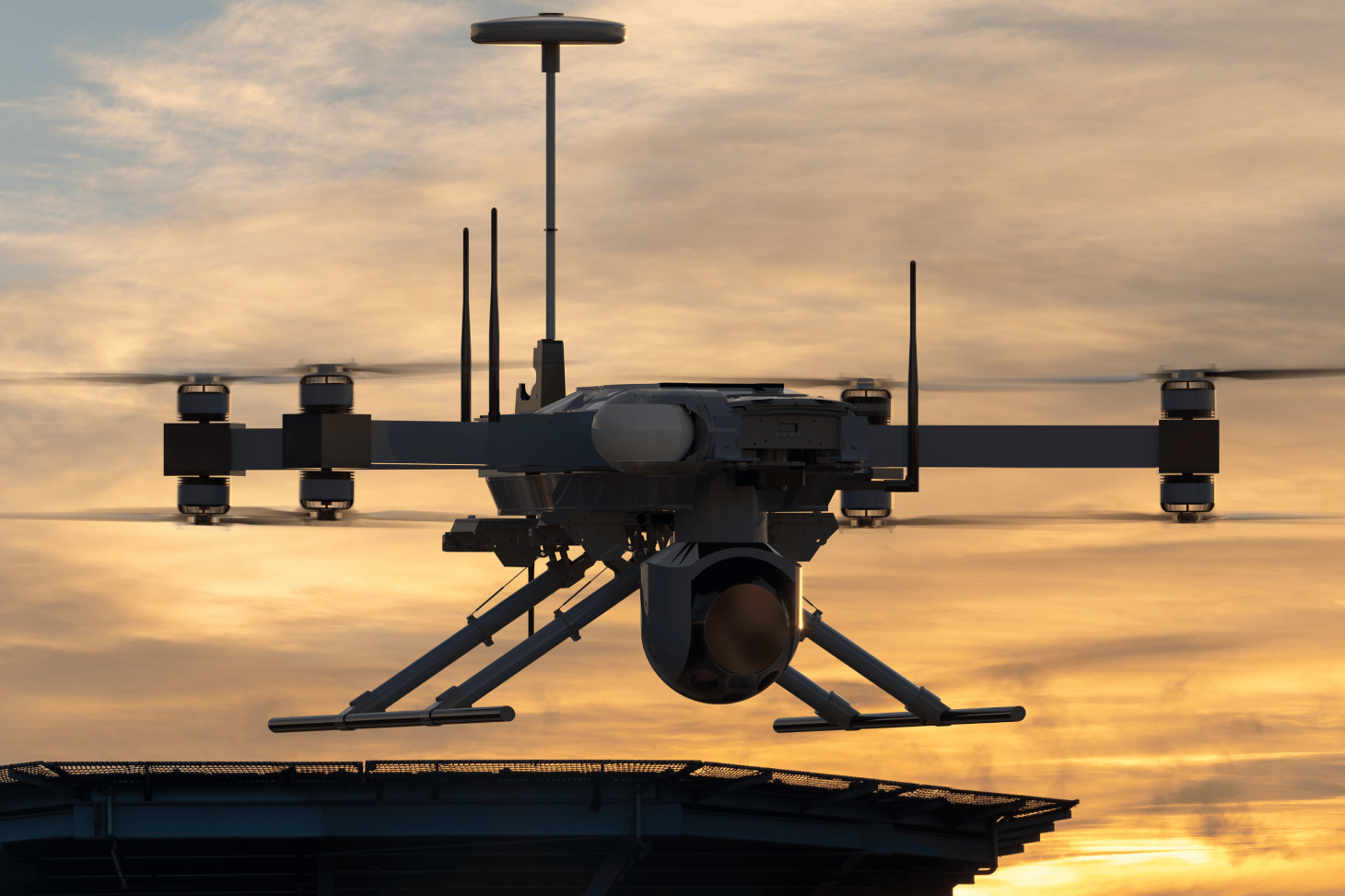
How 3D printing delivers benefits in aerospace
Topic
3D printing is often associated with the birth of rapid prototyping, giving engineers the tools to perfect designs without the need for specialist tooling or die sets.
Automotive parts production has really embraced the potential of 3D printing, with small to medium volume manufacturers in particular using additive manufacturing for everything from interior body panels to tooling for production. Engine parts, body parts and even chassis have all been the focus of 3D printing too, and we’ve already seen a range of fully 3D-printed concept cars, assembled from a 3D-printed skeleton.
However, while this remains a key function, 3D printing has evolved into much more than that – it’s now firmly a mainstream production method, delivering benefits for manufacturers and their customers across a wide range of sectors.
In the third part of our series exploring some of the sectors unlocking the greatest potential from 3D printing technologies, we discuss the benefits for aerospace and defence, one of the earliest adopters of additive manufacturing.
Of course, the main advantage for aerospace is the ability to reduce the weight of components, without compromising on strength or durability.
3D printing can boost efficiency and performance for the aerospace sector
3D printing is gaining traction as a manufacturing solution for lightweight yet robust components that help boost fuel efficiency and overall aircraft performance – enabling engineers to produce essential parts (including highly customised components, tailored to specific requirements) with precision, speed, and cost-efficiencies.
It also opens new opportunities for intricate and complex parts, that would be challenging or even impossible to achieve with traditional manufacturing methods. This can include intricate air ducts, structural metal components, bespoke wall panels and much more.
Metal aside, the aerospace sector uses resin printing materials like PA11 to create gauges, jigs, fixtures and placeholder parts for designers and OEMs within the aerospace supply chain.
If that’s not enough, aerospace component manufacturers and their customers also benefit from shorter lead times, in a sector where safety and efficiency matter more than ever.
Expediting the design-to-production timeline helps to ensure that innovative aerospace solutions can reach the testing and deployment phases more quickly, even in the most intricate, complex builds. But perhaps more importantly, rapid manufacturing also means spare parts can be produced and replaced at speed, on demand. This is equally as important in commercial aerospace, where lost time equates to lost profits.